CAPA Technical Writing: Corrective and preventive action (CAPA) entails documenting the processes for detecting, correcting, and preventing nonconformities in pharmaceuticals, medical devices, manufacturing, and food production. Precise, exact, and compliant paperwork is important to meet regulatory standards such as FDA, ISO, and GMP. Moreover, corrective and preventive action (CAPA) technical writing is essential in pharma sector to maintain compliance, quality, and regulatory adherence.
CAPA documentation aids in identifying the fundamental causes of quality issues and implementing corrective measures to prevent them from occurring again. Thus, here’s why CAPA technical writing is important in the pharmaceutical sector.
In terms of ensuring regulatory compliance, CAPA is very important. This helps to report what is required for compliance with: the USFDA (United States Food and Drug Administration, WHO-GMP guidelines, EU-GMP and the MHA etc. This means proper paperwork protects against regulatory warnings, penalties, and product recalls. Moreover, CAPA in pharma ensures the identification of manufacturing flaws, irregularities, or failures.
Its root cause analysis (RCA) is properly investigated and documented. Also, this is implementing preventive measures to avert future quality difficulties. As a result, it helps to maintain high quality pharma products while also ensuring patient safety. Thus, in the pharma industry, there is a huge importance of Corrective and Preventative Action (CAPA).
The importance of CAPA Technical Writing in the Pharmaceutical Industry
- Product Quality and Safety: Identifying the underlying causes of deviations and adopting corrective and preventive measures ensures that pharmaceutical goods are of high quality, safe, and effective. This also prevents contamination, mix-ups, and faults that could endanger patients.
- Risk Management: CAPA assists in proactively identifying and mitigating risks that may affect product development, manufacturing, and distribution. It also promotes a data-driven approach to quality assurance.
- Continuous Improvement: CAPA in pharma industry promotes a culture of continuous improvement by analyzing trends and applying best practices. This especially helps with process optimization and efficiency improvement.
- Customer Trust and Brand Reputation: Addressing and preventing quality issues consistently boosts consumer confidence while also maintaining the pharmaceutical brand’s integrity. This also stops costly recalls and legal concerns, which could harm the company’s reputation.
- Cost Reduction: Addressing quality concerns early using CAPA reduces waste, rework, and recalls, resulting in significant cost savings. This also helps to prevent production downtime and income loss.
Complete process flow of CAPA in the Pharma Sector
Step 2: Investigation and Root Cause Analysis (RCA): To determine the root cause, utilize the 5 whys method, a fishbone diagram, or an FMEA.
Step 3: Implementing CAPA: Define precise measures to correct and prevent recurrences.
Step 4: Check for Effectiveness: Check to see if the problem has been permanently resolved.
Step 5: Documentation and Closure: CAPA facts should be recorded in SOPs (standard operating procedures) and submitted as regulatory reports.
Benefits of CAPA in the Pharmaceutical Industry
- Effective Problem Solving: A methodical approach to identifying root causes guarantees that problems are specifically resolved.
- Regulatory Readiness: Showcases a proactive quality system to regulatory authorities, lowering the likelihood of compliance failures.
- Data-driven Decision Making: It predicts and prevents problems using real-time monitoring and data analytics.
- Operational Efficiency: Streamlines manufacturing and also quality control procedures to reduce errors and delays.
- Workforce Accountability: We ensure that our staff adheres to tight protocols and corrective actions, establishing a quality oriented work culture.
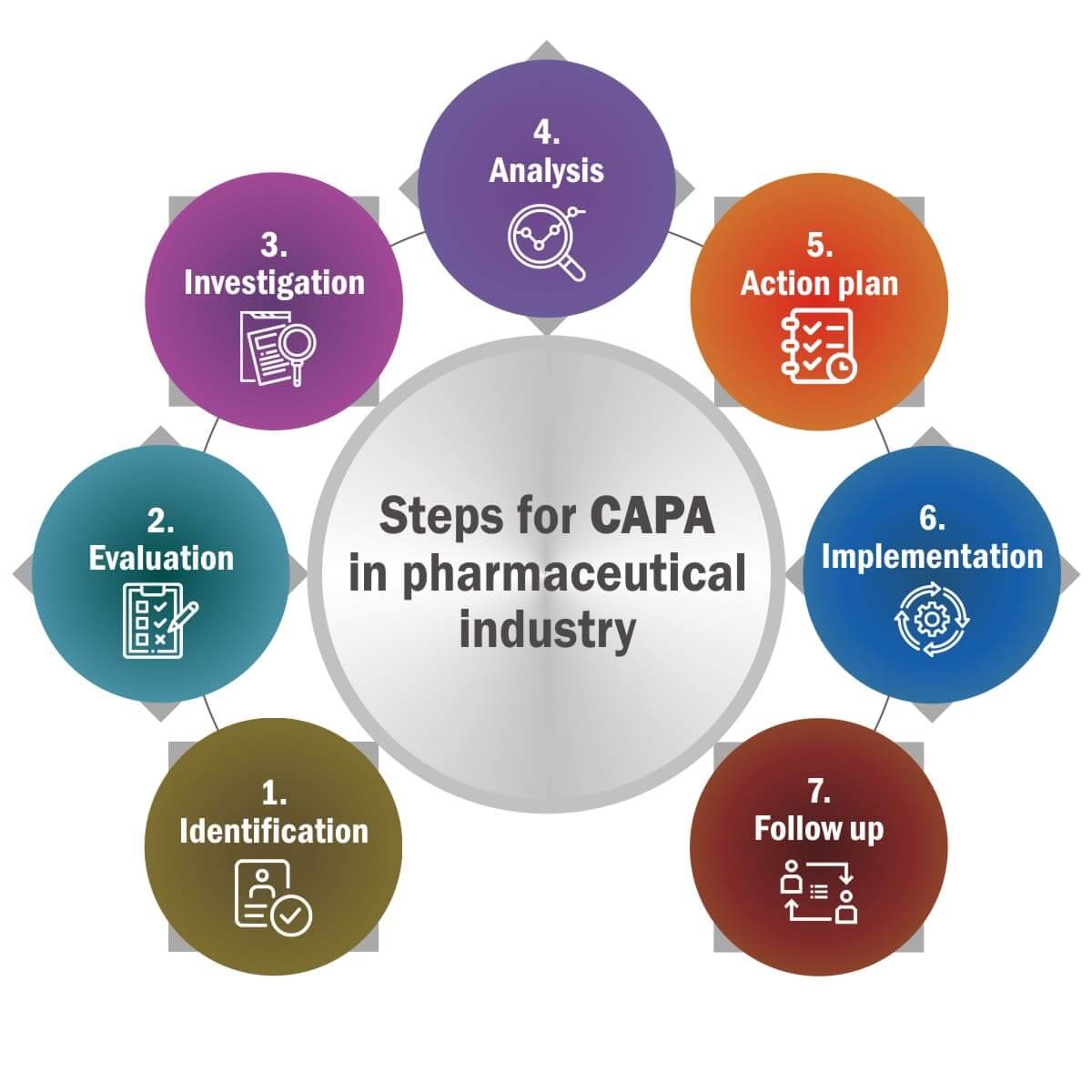
The Bottom Line
At last, corrective and preventative action (CAPA) plays an important role and gives many benefits to the pharma manufacturing industry. This helps manufacturing companies to take every right step while making the pharma products. In this context, Knors Pharma Solutions LLP plays an important role by offering CAPA technical writing services to pharma companies. For pharma professionals, this is the right moment to know more about these services with the help of Knors Pharma.
Related FAQs
CAPA (corrective and preventive action) is a quality management procedure in the pharma business that identifies, investigates, and resolves deviations, nonconformities, or possible hazards.
What is the purpose of the CAPA?
The main objective of CAPA is to:
- Address current quality flaws (corrective action)
- Prevent the occurrence of comparable situations (preventive action)
- Ensure regulatory compliance
- Increase operational efficiency and patient safety
In the CAPA systems, Knors Pharma has particularly included:
- Problem identification (deviation, complaint, oos, audit findings)
- Investigation and root cause analysis
- Corrective and preventive action plan
- Implementation and verification of effectiveness
- Documentation and closure